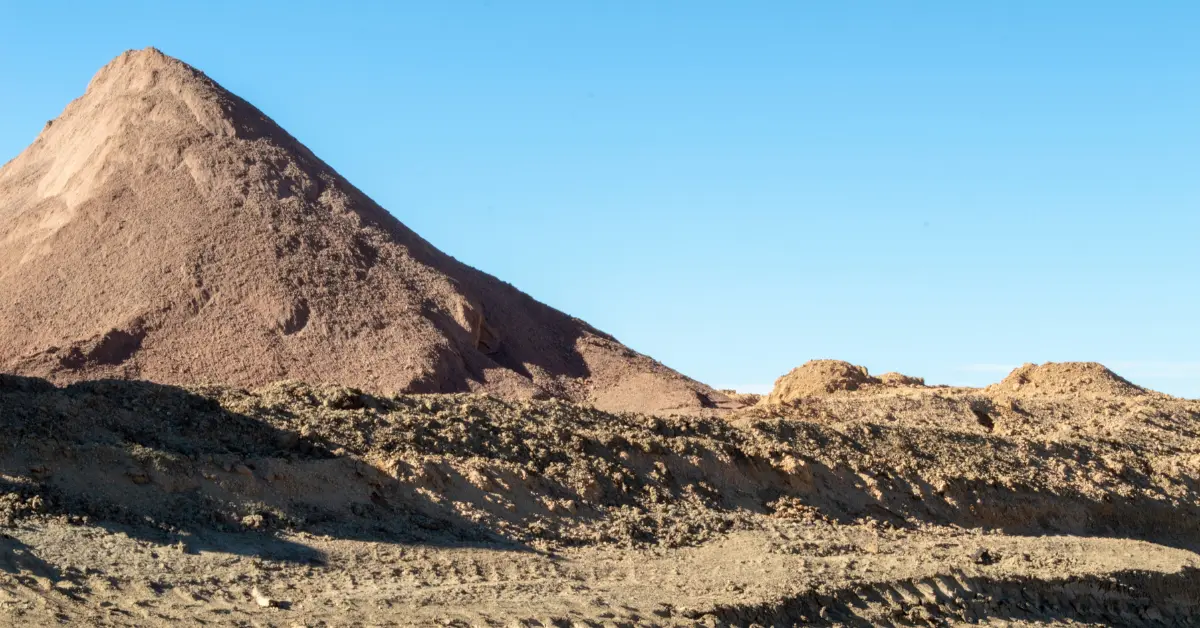
In construction projects, the materials used beneath the surface are just as important as those placed above it. One of the most vital materials is select fill dirt, a specific type of soil chosen for its stability and consistency. This material is screened and prepared to meet specific standards that support strong foundations. It typically contains minimal organic matter and has a well-balanced composition that allows for effective compaction. Builders prefer this type of fill because it creates a firm and even base, reducing the chances of shifting or settling over time. Using the correct fill material from the start can help avoid costly repairs and ensure the long-term durability of the structure.
Core Advantages of Using Select Fill Dirt
Superior Stability
This type of soil is processed to have uniform particle sizes, allowing it to pack down tightly when placed and compacted. A stable base helps keep the foundation level and prevents movement beneath the structure. When the soil beneath a building shifts, it can lead to serious issues, such as cracking or sinking. With the right fill material, the soil stays firm, holding its shape under the weight of the building. Proper compaction also improves load-bearing capacity, making the ground more resistant to pressure from heavy equipment and structures.
Reduced Risk of Settlement
Settlement happens when the ground under a structure sinks or compresses unevenly. This is often caused by using poor-quality soil or failing to compact the material properly. By using reliable fill dirt for construction, builders can reduce the chance of these problems. Select fill is carefully chosen for its consistency, with fewer voids or soft spots that might allow the ground to settle after construction. When the soil is consistent throughout, it provides the same level of support across the entire foundation area.
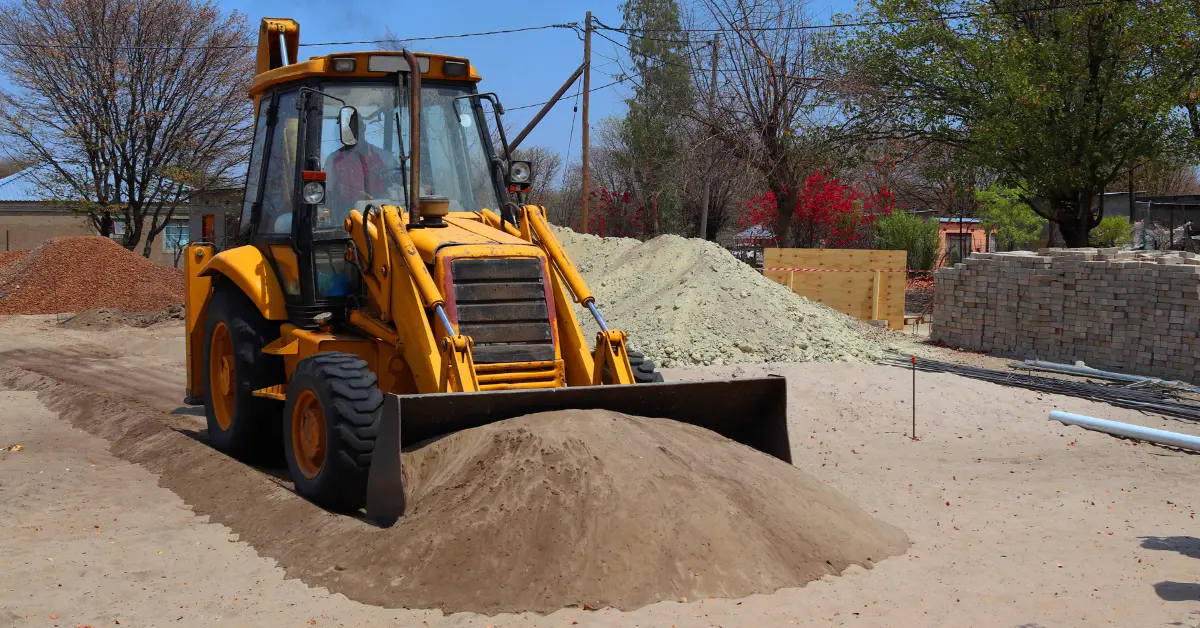
Effective Drainage and Moisture Control Features
Good drainage is a crucial factor in protecting any foundation from moisture-related issues. When builders select dirt for foundations that is designed to handle water flow effectively, they prevent problems like erosion, pooling, or water pressure buildup against the structure. Select fill dirt often includes a mix of materials that allows water to pass through or drain away efficiently, without trapping moisture close to the building. This keeps the foundation dry and reduces the risk of water damage, which can weaken the structure over time. Soil with proper drainage properties also helps avoid frost heave in colder climates, where frozen water in the ground can push against the foundation and cause movement.
Minimizing Organic Content
Roots, leaves, or plant debris can cause major issues when used beneath a building. This material breaks down, resulting in gaps or voids within the soil. This is why fill dirt delivery for foundation work should always involve materials with low organic content. Select fill dirt is specifically screened to remove these unwanted elements, making it much more reliable for supporting heavy structures.
Comparing Select Fill Dirt to Other Soil Types
Topsoil and Nutrient-Rich Soils
While topsoil is excellent for planting and landscaping, it is not suitable for building foundations. One reason is that topsoil contains high amounts of organic matter, which can break down over time, causing the soil to lose volume. This characteristic makes it a poor choice compared to dirt for building projects that require stability and compaction. Nutrient-rich soils are soft and loose, designed to support plant life, not heavy structures. Using this kind of soil beneath a building can lead to uneven settling, shifting, or even structural failure.
Understanding the Impact of Particle Size and Clay Content
Fill material with too much clay tends to hold water, which can lead to swelling or shrinking as moisture levels change. On the other hand, soil that contains balanced particle sizes compacts better and drains more efficiently. Bulk fill dirt that is screened and appropriately processed reduces the risks associated with excessive clay content.
Screened Fill Dirt
One of the key reasons builders prefer screened fill dirt is the reliable gradation it offers. Gradation refers to the distribution of different particle sizes within the fill material. Consistent gradation allows for even compaction, reducing the likelihood of voids or weak areas in the soil base. Larger rocks and debris are removed, leaving behind soil that is smoother and more uniform in texture. It makes the compaction process faster and more effective, helping crews achieve the desired soil density with less effort.
Ordering and Transporting Select Fill Dirt Efficiently
Choosing the Right Supplier
When sourcing soil for site preparation, it is essential to work with reputable suppliers who can guarantee the quality of the materials they provide. Here's what to consider when selecting a supplier:
- Certification of Materials: Look for certificates from recognized bodies such as ASTM International or local regulatory agencies. These documents should include details about soil composition, contaminant levels, and compliance with environmental standards. A valid certification tells you that the supplier’s soil has been tested in an accredited lab under controlled conditions. It also shows the supplier’s commitment to transparency and quality. When certifications are current and detailed, you can plan your project with confidence, knowing the fill dirt will behave predictably under compaction. Always verify that the certificates list the exact test methods and dates. Do not accept generic claims of “certified” without accompanying reports.
- Screening and Grading Processes: Good suppliers use mechanical screens or trommels that filter soil particles to a uniform size. They may also employ air classifiers or wet screening systems to eliminate fines or clay lumps. A detailed grading process will list the percentage of particle sizes retained on various mesh screens. This information helps you understand how the soil will compact and drain. Clean, well-graded fill reduces the risk of uneven settlement and improves load-bearing capacity.
- Testing Reports Availability: Testing reports should cover moisture content, Atterberg limits, particle size distribution, and compaction characteristics. These tests reveal how the soil will respond to water and mechanical forces. For instance, moisture content determines the ease of compaction, while particle size distribution influences drainage rates. A supplier that offers digital or printed reports for each batch demonstrates a commitment to data-driven quality control. You can use these reports to confirm the soil matches your engineer’s specifications before delivery. It is reasonable to request recent test dates and specific batch numbers. Suppliers with robust reporting systems often have a trained laboratory staff and a dependable quality assurance program.
- Delivery Capabilities: Even the highest-quality fill dirt is useless if it arrives late or in uneven batches. Evaluate a supplier’s delivery fleet size, scheduling flexibility, and geographic reach. Reliable suppliers will offer multiple truck sizes and track each load with GPS. They can adjust to weather delays or permit changes without disrupting your timeline. Confirm their loading procedures to avoid cross-contamination between different soil types. Ask about backup plans in case of equipment failure. A supplier with consistent delivery records will share on-time performance data. They may also provide online portals for scheduling and real-time delivery tracking.
- Reputation and Experience: Pay attention to feedback on product consistency, communication, and problem resolution. Suppliers who have worked on a range of commercial, residential, or infrastructure sites will better anticipate challenges. Industry partnerships and certifications, such as membership in local builders’ associations, can further validate their standing.
This due diligence will help ensure landscaping soil options meet project needs and that your work proceeds on time and within budget.
Calculating Volume Needs
Correctly estimating the amount of material needed for a construction project helps avoid shortages or costly overordering. When buying dirt in bulk, understanding how much fill is required for your specific site is critical. Volume needs are usually calculated based on the area’s dimensions, including length, width, and depth. It’s also important to factor in compaction rates, since soil volume decreases as it is compressed during placement. Taking the time to calculate these figures ensures that the right amount of soil arrives on-site, reducing the chance of interruptions. Coordinating deliveries effectively is just as important as selecting the right type of soil. If you need dirt delivered at specific stages of your project, it’s helpful to plan ahead and communicate clearly with the supplier. Large-scale projects often require multiple truckloads of fill, so organizing a delivery schedule helps prevent downtime and keeps the job moving forward. Arranging proper unloading zones and confirming timing with all involved teams will reduce confusion and help maintain site safety.
Managing the Cost of Select Fill Dirt
Budgeting for order fill dirt involves more than just the price per cubic yard. To control costs, it is important to consider how much material is needed and the size of the delivery vehicles. Larger truckloads may reduce delivery fees per unit of soil, but they require sufficient space on-site for unloading. Delivery timing also affects expenses; rush orders or off-hour deliveries may come with additional charges. Comparing quotes from several fill dirt companies helps identify the best value for your project’s needs.
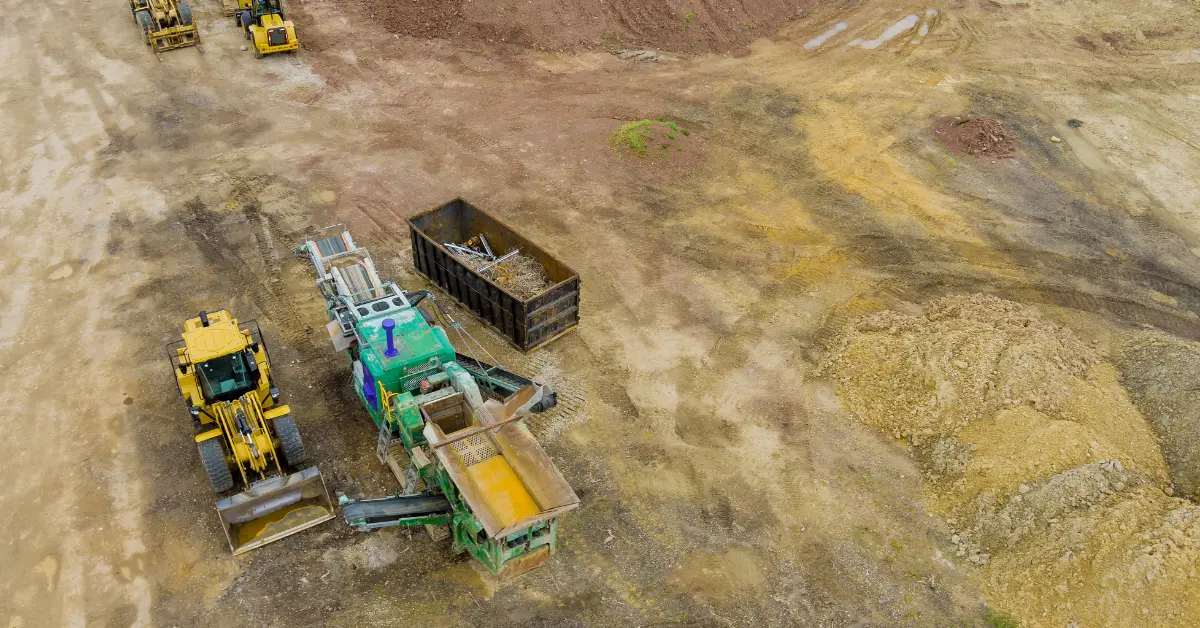
Best Practices for Placing and Compacting Select Fill Dirt
Preparing the Site
A successful foundation project begins with thoughtful site preparation before any soil is placed. Here are the steps to follow:
- Remove All Surface Debris: Inspect the entire area to identify and remove visible obstacles such as old concrete slabs, broken pavement, tree stumps, and large rocks. Use mechanical equipment combined with manual tools such as rakes and shovels to extract roots and woody material that could decompose under new fill. Organic matter left behind can settle unevenly over time, resulting in voids and instability within the fill layer. Dispose of debris according to local regulations to prevent contamination. After larger debris is cleared, walk the site to catch smaller items like branches or glass fragments that pose hazards for workers and machinery.
- Verify Subgrade Conditions: Once surface debris is removed, it’s essential to assess the existing soil layer to confirm it meets firmness and stability requirements. Conduct a visual inspection for soft spots, muddy patches, and areas where previous excavation may have disturbed the soil structure. Use a handheld penetrometer or light-proof rolling equipment to test compaction levels at multiple points across the site. If the subgrade shows signs of excessive moisture or lack of cohesion, allow it to dry or stabilize before adding fill. In areas where the soil is too loose or was recently backfilled, consider adding a thin layer of granular material and re-compacting to achieve a uniform density. Record these test results and compare them against your engineer’s specifications for load-bearing capacity.
- Check for Proper Drainage Slope: Ensuring correct drainage slopes around the foundation area is vital to protect the fill and underlying structure from water damage. After verifying the subgrade, use a transit level or laser level to establish a gentle slope directed away from the planned foundation footprint. This slope encourages surface water to flow toward designated drainage channels or retention basins rather than pooling near footings. Mark high and low points with stakes and string lines to guide grading equipment.
- Mark Boundaries Clearly: Refer to project blueprints to locate property lines, setbacks, and foundation limits. Use brightly colored flags, spray paint, or surveyor’s tape to create a visible perimeter. Place stakes at regular intervals—no more than 10 feet apart—along each boundary line and affix string or laser-guided lines between them. This visible guide helps equipment operators maintain straight, level cuts and fills. Include markers for utilities and underground features to avoid accidental damage during grading. If the site has irregular shapes, plot additional control points at the corners and along the curves.
- Test Soil Moisture Content: Take samples at various locations across the site and use a portable moisture meter to measure water content on the spot. Alternatively, perform a standardized field test by weighing soil samples before and after oven drying. Compare these values against the optimum moisture range specified by your geotechnical engineer. Moisture levels outside the ideal window can lead to poor compaction, increased voids, and potential settlement. If the soil is too wet, postpone placement and allow it to dry naturally or use mechanical dewatering methods. If too dry, lightly mist the area with water and let it absorb before compacting.
- Coordinate with Delivery Timing: As emphasized previously, communicate your projected clearance and grading completion date to the supplier, then schedule deliveries in manageable increments to avoid overloading the site. Confirm the supplier’s capacity for timely deliveries, taking into account potential delays due to weather or traffic. Establish a clear window for clean fill delivery trucks to arrive, unload, and depart without interfering with other site operations.
Thorough site preparation is crucial for achieving a uniform and stable base for fill dirt placement.
.webp)
In every stage of preparing a building site, the choice of fill dirt plays a key role in the overall success of the project. Working with trusted clean fill dirt suppliers, confirming soil specifications, and managing deliveries efficiently all contribute to a smooth construction process. Whether ordering bulk fill dirt for a large-scale development or sourcing material for a smaller project, these steps make a significant difference. Choosing the right soil helps prevent problems that can impact the long-term safety of a structure. Staying informed about types of soil for grading and their proper uses gives contractors the knowledge they need to make the best decisions for each job.